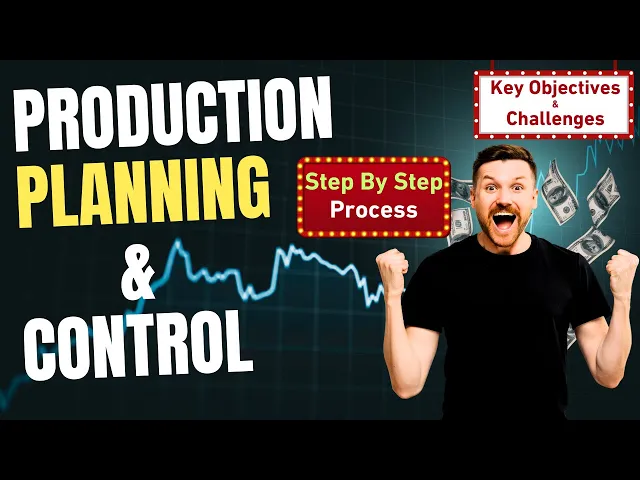
Production Planning and Control in ERP
Digital Transformation
Jul 1, 2025
Explore how ERP systems enhance production planning and control, driving efficiency and customer satisfaction in manufacturing.
Production planning and control (PPC) in ERP systems ensures manufacturing runs smoothly by aligning resources, streamlining processes, and improving decision-making. Here's what you need to know:
What It Does: PPC in ERP systems automates scheduling, tracks inventory in real-time, and optimizes production to meet demand efficiently.
Key Benefits:
Reduced lead times (up to 95%).
Lower inventory costs (75% of companies report savings).
Improved efficiency (up to 30% increase).
Core Features:
Material Requirements Planning (MRP): Automates inventory and procurement.
Master Production Scheduling (MPS): Creates detailed production plans.
Real-Time Adjustments: Adapts schedules instantly to disruptions.
With industry-specific tools, ERP systems handle unique challenges like compliance in food manufacturing or just-in-time (JIT) processes in automotive production. Companies adopting ERP-driven PPC report better customer satisfaction, lower costs, and smarter decision-making through real-time data.
ERP systems are now considered essential for manufacturers to stay competitive in today’s fast-paced market.
Production Planning and Control | Step By Step Process | Key Objectives and Challenges | MRP | MPS
Main Features of Production Planning and Control in ERP
ERP systems offer manufacturers tools that simplify planning, scheduling, and production control. These features work together to create a streamlined manufacturing process that adapts quickly to changes while maintaining efficiency and quality. Let’s break down some of the key features that make this possible.
Material Requirements Planning (MRP)
Material Requirements Planning (MRP) is the cornerstone of production planning in ERP systems. It calculates the materials and components needed to manufacture a product, automating the complex task of determining what’s required, when it’s needed, and in what quantities.
The MRP process involves three main steps: assessing current inventory, identifying additional material needs, and scheduling their purchase or production. This ensures that materials are available precisely when needed, keeping production on track.
MRP integrates several critical inputs to eliminate guesswork and prevent stockouts:
Input | Purpose |
---|---|
Bill of Materials (BOM) | Details the components required for production |
Master Production Schedule (MPS) | Outlines when products need to be produced |
Inventory Records | Tracks current stock levels |
By automating procurement and inventory management, MRP accelerates production. This has played a key role in making consumer goods more accessible and affordable.
To ensure MRP works effectively, manufacturers should maintain an up-to-date bill of materials and ensure real-time visibility into inventory levels across the organization. These practices help forecast supply needs accurately and keep operations running smoothly.
Master Production Scheduling and Capacity Management
Master Production Scheduling (MPS) serves as the blueprint for manufacturing activities, determining what to produce, in what quantities, and when. ERP systems use MPS to create a detailed production plan.
MPS relies on various demand inputs, such as open production orders, sales orders, and forecasts, to generate schedules that align with both market demand and available resources. ERP systems can even adjust MPS automatically when forecasts or delivery schedules change.
Tools like finite capacity scheduling factor in available labor, equipment costs, inventory levels, and machine availability to optimize production schedules. ERP systems also support "what-if" scenarios, allowing manufacturers to evaluate different production strategies and their impact on resources. For longer-term planning, Rough Cut Capacity Planning (RCCP) helps address capacity needs and make necessary adjustments if resources fall short.
Real-Time Schedule Adjustments and Workflow Management
In manufacturing, the ability to quickly adapt to unexpected changes is crucial. ERP systems provide real-time visibility into inventory, equipment status, and workforce capacity, enabling automated alerts and instant schedule adjustments during disruptions. This eliminates reliance on outdated information and ensures smooth operations across the production process.
The benefits are clear: ERP systems can reduce production delays by up to 30% and boost customer satisfaction by 25%. These improvements come from the system’s ability to detect bottlenecks before they escalate.
Additionally, ERP systems offer insights that help managers allocate resources more effectively, such as monitoring machine availability, workforce capacity, and material supply. By automating routine tasks, employees can focus on higher-value strategic activities. To maintain the reliability of these adjustments, manufacturers should establish data governance frameworks that ensure accurate and consistent data management.
Industry-Specific Production Planning Requirements
ERP systems, at their core, provide essential tools for production planning. But when it comes to different industries, these systems need to adapt to unique challenges, regulations, and operational demands. Let’s take a closer look at how ERP systems cater to specific industries.
Automotive Manufacturing
In automotive production, Just-in-Time (JIT) manufacturing is a game-changer. This approach requires flawless coordination between suppliers and production facilities to keep assembly lines running smoothly. ERP systems make this possible by offering real-time supply chain visibility and automating procurement processes, ensuring materials arrive exactly when they’re needed.
Take, for example, a mid-sized Canadian drivetrain component supplier. After adopting an ERP solution, they slashed inventory levels by 24% and improved scheduling efficiency by 40%. The results can be even more striking - companies implementing JIT through ERP systems have reported inventory reductions of up to 75%, cutting out warehousing costs altogether. Zara SA famously sums up this philosophy with their mantra: "inventory = death".
Key ERP features for automotive manufacturers include:
Real-time supplier coordination across multi-tier networks
Automated demand forecasting to avoid production halts
Compliance tracking for meeting strict industry regulations
IoT integration for live production line and inventory updates
While automotive manufacturers focus on efficiency and precision, food manufacturers rely on ERP systems to ensure safety and quality at every step.
Food Manufacturing
Food production comes with its own set of challenges - batch tracking, expiration management, and strict regulatory compliance are non-negotiable. ERP systems tailored for this industry step in to ensure safety and quality while streamlining operations.
These systems often include features like HACCP integration, allergen management, and shelf-life tracking. Such tools help with accurate labeling, prevent cross-contamination, and enable swift action during recalls by automating quality checks and tracking issues.
One example is Castle Importing, which used SAP Business One to gain complete oversight of its production processes. The system integrated purchase orders, production, invoicing, and shipping, while real-time financial data and quality management improved traceability. Similarly, Morrison Meats automated inventory updates via barcode scanning and received low-stock alerts, eliminating the need for manual spreadsheets.
The benefits of ERP systems in food manufacturing are clear: 94% of organizations report improved operational efficiency, and 64% see better inventory accuracy.
Machinery and Equipment Production
Manufacturing machinery and equipment often involves custom orders, complex configurations, and extended lead times. These unique demands require specialized ERP features to manage production effectively.
ERP systems in this sector excel at streamlining custom configurations and pricing while minimizing errors. CAD2BOM functionality is a standout feature, converting 3D CAD models into bills of materials automatically. This saves time for engineers and ensures accuracy throughout the production process.
Advanced planning and scheduling tools are crucial for managing long lead times, while real-time inventory control prevents material shortages. IoT integration further enhances operations by providing insights into machine performance and material conditions. This connectivity allows manufacturers to optimize workflows and allocate resources more effectively.
A great example is Reelex, an equipment and packaging manufacturer. By implementing Genius ERP, they addressed their complex manufacturing needs with a tailored solution.
Key ERP features for machinery manufacturers include:
Real-time job costing for analyzing project profitability
Engineering tools, such as CAD integration and change management
Supply chain management for sourcing components from multiple vendors
Quality systems to meet precision manufacturing standards
For machinery manufacturers dealing with custom orders and intricate designs, ERP systems bring everything together, reducing manual tasks, improving efficiency, and ensuring all processes align seamlessly. This level of integration is essential for staying competitive and profitable in today’s market.
Transform Your Business with W4 Martech
Leverage advanced digital marketing and IT solutions to expand your reach into the Chinese Market, streamline operations, and enhance customer interactions. Explore tailored services like Odoo consultancy, DevOps, and ChatGPT integration to drive growth and efficiency.
Benefits of ERP Production Planning and Control
When manufacturers integrate production planning and control with ERP systems, the results are striking. These systems reshape operations, delivering measurable gains in efficiency, customer satisfaction, and decision-making. The impact highlights how ERP-driven production planning can elevate manufacturing performance.
Improved Efficiency and Lower Costs
ERP production planning systems simplify manufacturing workflows and cut down inefficiencies, leading to impressive gains in lead times and overall efficiency. For instance, manufacturers using ERP systems with real-time, accurate data have reported a 23% reduction in costs and a 22% drop in administrative expenses.
By centralizing processes, ERP systems streamline scheduling and inventory management, reducing delays and waste. They also make resource allocation more precise. This means better workforce scheduling, fewer machine downtimes through improved maintenance planning, and the elimination of costly manual errors. According to the Department of Energy, manufacturers using real-time energy monitoring via ERP systems can cut energy usage by 10-30%.
One standout example is a semiconductor manufacturer that implemented real-time analytics across its production facilities. Within six months, the company boosted its yield by 9.3%, adding approximately $15 million in annual revenue per facility and slashing production costs by 7.2%.
These efficiency improvements don't just save money - they also enhance product quality and delivery reliability.
Better Customer Satisfaction
ERP production planning systems ensure on-time deliveries, precise scheduling, and efficient resource use, all of which build customer trust. When manufacturers consistently meet delivery deadlines and maintain high product quality, customer relationships thrive.
Take the automotive industry as an example. A major manufacturer used real-time analytics to fine-tune its assembly operations, analyzing over 500 variables. Within a year, the company reported a 23% drop in assembly defects, a 15% boost in throughput, and a 19% reduction in unplanned downtime. These improvements resulted in $42 million in annual savings across three plants.
ERP systems also allow businesses to provide accurate delivery timelines and live order status updates. If production schedules shift due to material delays or equipment hiccups, automated updates keep customers informed, helping them plan more effectively and reinforcing trust.
Beyond customer satisfaction, real-time data is transforming how manufacturers make decisions and improve processes.
Real-Time Data and Process Improvement
Access to real-time data in ERP production planning shifts decision-making from reactive guesswork to informed action. ERP systems gather data from multiple sources - like sales records, IoT devices, and sensors - giving manufacturers a real-time snapshot of their operations. This ensures that everyone in the organization is working with the same, up-to-date information, enabling quicker and smarter decisions.
The productivity gains are substantial. Manufacturers using real-time data to guide decisions have seen productivity improve by as much as 30%. Additionally, companies leveraging real-time analytics report an 18% boost in Overall Equipment Effectiveness (OEE), a 13% drop in unplanned downtime, and a 7% reduction in manufacturing cycle times.
Real-time monitoring helps production managers spot bottlenecks, such as slow workstations, low material inventory, or underperforming equipment. By identifying trends, benchmarking performance, and using predictive models, manufacturers can continuously refine processes. When paired with machine learning and AI, real-time data also enables more accurate and dynamic demand forecasting.
It’s no surprise that 77% of manufacturers believe real-time data and analytics are essential for improving operational efficiency and cutting costs.
Best Practices for ERP Production Planning Implementation
Making the most of ERP production planning hinges on following key strategies that optimize your system and enhance operational performance.
Keep Data and Bill of Materials (BOM) Accurate
Accurate data is the backbone of successful ERP production planning.
Start by establishing strict data governance protocols. Assign dedicated data stewards and implement clear standards to maintain the quality of information flowing into your ERP system. This helps prevent errors and ensures your data remains reliable over time.
BOM accuracy is equally critical. Regularly audit and update BOMs to match current product designs and material specs. Collaborative reviews and version control are essential to keep everything aligned. Training employees on proper data entry practices is another must. Combine this with robust validation rules at the point of entry to catch issues early. Many modern ERP systems take this a step further, offering real-time error detection and automated validation features. As Thomas Hoferer from DOLL Fahrzeugbau GmbH put it:
To maintain long-term data accuracy, automate validation processes and schedule regular data cleanups to tackle inconsistencies, duplicates, and outdated information. Standardizing data formats across departments ensures everyone operates on the same page.
Use Data Analytics for Demand Forecasting
Accurate data is just the start - proactive demand forecasting is the next step. Advanced ERP analytics can refine forecasting accuracy, leading to smarter production decisions and better customer service.
ERP systems pull data from multiple sources - sales, procurement, inventory, finance, and customer service - into one platform. This integrated approach allows for comprehensive forecasting models that consider all factors influencing demand. In fact, ERP-driven forecasting can improve accuracy by 10% to 20% compared to traditional methods. Even a 1% boost in accuracy can reduce lead times, optimize inventory, and increase profit margins.
By using built-in statistical models, you can automate forecasts and eliminate the need for error-prone manual spreadsheets. Real-time updates and version control ensure your predictions are always current.
Scenario planning is another game-changer. Use your ERP system to simulate different demand scenarios - seasonal trends, promotional impacts, or unexpected market shifts. This preparation helps you craft flexible production plans that can handle diverse conditions.
Segmenting forecasts by region, sales channel, product line, or customer group provides even more precision. Understanding the unique demand patterns across these segments allows for tailored strategies that further improve overall accuracy.
The financial impact of data-driven forecasting is substantial - companies can see gains of up to $85 million over five years through reduced inventory costs, better customer service, and optimized resource use.
Adjust to Market and Operational Changes
ERP systems shine when it comes to adapting to change. In today’s unpredictable manufacturing landscape, flexibility is not just helpful - it’s essential.
Dynamic scheduling tools within ERP systems allow you to adjust production plans in real time. By using data from GPS, IoT devices, and sensors, you can respond quickly to urgent requests, equipment failures, or supply chain disruptions.
Scenario planning also plays a role here. Modeling various outcomes helps you identify the best resource plans under different constraints, ensuring you're prepared for whatever comes your way.
Set up clear trigger points to signal when adjustments are needed. Real-time monitoring of these triggers ensures swift action, minimizing disruptions and keeping operations running smoothly.
To make the most of these tools, invest in team training. Pilot projects and hands-on sessions will help your staff get comfortable with dynamic scheduling processes before rolling them out on a larger scale. Scalable ERP solutions also provide the flexibility to manage varying workloads and resource demands.
Looking ahead, by mid-2026, large organizations are expected to redesign workflows around AI, which could boost efficiency by up to 45%. Businesses that adopt flexible, data-driven production planning today will be better positioned to leverage these advancements.
Finally, continuous improvement is key. Regularly review scheduling performance, gather feedback from your team, and make incremental updates to keep your ERP production planning system delivering value in an ever-changing market.
Conclusion
ERP-driven production planning and control is reshaping manufacturing by significantly reducing lead times by as much as 95% and cutting inventory costs for 75% of organizations. These improvements lay the groundwork for a complete transformation of operational efficiency.
Modern ERP systems bring everything together. They unify business processes, centralize data, and offer real-time insights across all manufacturing activities. Whether it’s precise material planning or flexible scheduling, these systems simplify operations, allowing manufacturers to adapt quickly to market changes while upholding quality standards and meeting regulatory requirements.
For many organizations, the impact of ERP adoption is clear: up to 30% efficiency gains, with 95% of businesses benefiting from shorter process cycles and better collaboration. These enhancements directly improve customer satisfaction by enabling faster order processing, on-time deliveries, and superior service quality.
Industry-specific challenges like navigating complex supply chains in automotive manufacturing, ensuring food safety standards, or managing intricate project timelines in machinery production become far more manageable with ERP solutions tailored to address these needs. The adaptability of modern ERP systems means businesses can scale and handle growing complexities without sacrificing performance.
It’s no wonder that over 70% of manufacturers now consider ERP essential to their operations. By driving data-based decisions and streamlining processes, ERP systems are helping businesses gain a competitive edge.
Adopting a robust ERP solution isn’t just a smart move - it’s a strategic necessity. W4 Martech Technology For Business specializes in helping manufacturers harness the full potential of ERP through expert Odoo consultancy and implementation services. By offering tailored solutions, system optimization, and business process consultancy, W4 Martech ensures that businesses can overcome production planning and control challenges effectively. Their proven methods empower manufacturers to achieve operational excellence and unlock growth opportunities in today’s demanding market.
A well-implemented ERP system integrates seamlessly with current operations and provides the flexibility needed to adapt and thrive in an increasingly competitive landscape.
FAQs
How can an ERP system streamline production planning and control?
An ERP system simplifies production planning and control by bringing together data from critical areas like inventory, supply chain, and manufacturing into one centralized platform. This integration gives managers real-time access to precise information, helping them make quicker and smarter decisions.
Using an ERP, businesses can better schedule production, track workflows, and allocate resources to cut down on downtime and lower expenses. By providing greater visibility into operations, companies can boost productivity, meet deadlines more consistently, and respond swiftly to changing demands, making the manufacturing process smoother and more efficient.
What challenges do ERP systems solve for food manufacturers?
ERP systems tackle some of the biggest hurdles food manufacturers face. They offer real-time inventory tracking, ensure lot traceability to uphold safety and quality, and help manage compliance with strict food industry regulations. Beyond that, they help minimize quality inconsistencies, safeguard sensitive data, and simplify complex supply chain operations.
By automating workflows and consolidating data into a single platform, ERP systems help manufacturers boost efficiency, maintain consistent product quality, and respond swiftly to evolving industry needs.
How can manufacturers maintain accurate data and bills of materials (BOM) in their ERP systems?
To keep bills of materials (BOM) and other data accurate in ERP systems, manufacturers can adopt several practical strategies:
Use data validation processes to catch errors and inconsistencies in BOM entries before they cause issues.
Conduct routine data reviews to eliminate outdated or incorrect information.
Develop clear and standardized data entry procedures to reduce the chances of human errors.
Leverage ERP tools to automate tasks like tracking changes and identifying discrepancies, ensuring updates are precise and well-documented.
Focusing on these practices helps manufacturers minimize production errors, boost efficiency, and maintain seamless operations.